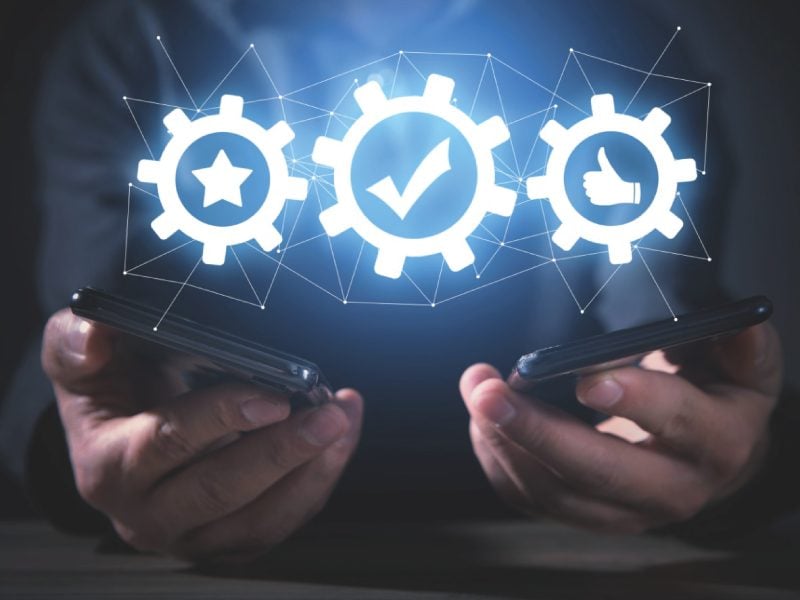
3M (Muda, Mura, Muri)of Lean Application
In lean applications, 3M (Muda, Mura and Muri) are Japanese words describing the unplanned, irregularities and wastes in production. It is used in lean applications and within the scope of Toyota production system studies in our country. Quantification of losses, complexity in the lack of visualization of waste; Muda, Muri and mura, which represent the essence of waste, can be solved by careful research.
Toyota has identified 3 main types of waste: Muda-Muri and Mura. These three MU’s are strongly interconnected and epitomize the Japanese sense of waste. These seemingly separate terms actually contribute to the success of the Toyota Production System, and it has been developed to eliminate these 3 enemies of lean manufacturing.
1. Muda (Non Value Add)
Shortly, Muda means waste. Muda means wastage resulting from unnecessary activities. This type of waste refers to the use of time, money and resources that do not add value to the customer. Muda reveals which steps are necessary for the process and which need to be reduced or eliminated. There are 7 Mudas
1.1. Overproduction
Producing more than the next process or customer needs. He is known as the worst of the other Mudas. Because it contributes to the other 6 mudas
1.2.Waiting
It is the idle waiting of the operators during the operation of the machines, the failure of the equipment, the delay of the necessary parts.
1.3. Convayance
Unnecessary transport movements. For example, piling up the material to be transported, taking it to the warehouse and bringing it back, accumulating somewhere, etc.
1.4. Overprocessing
It is the unnecessary processing on the parts due to unnecessary and wrong process.
1.5. Inventory
It is a stock muck that occurs as a result of a Standby, Repair, Overproduction muda.
1.6.Motion
They are unnecessary movements such as looking at parts, equipment, documents. It covers all kinds of human and equipment movement without added value.
1.7. Correction
It is the rework of defective material or the reproduction of defective material.
Due to the above-mentioned Mudas, businesses unnecessarily lose people, materials and energy. Mudas cause losses and make it difficult to deliver the product at the right time.
2.MURİ (Overburden-Unreasonableness)
Muri means overload. It is an equipment overloaded beyond its capacity or a waste of human resources. An overloaded employee becomes unnecessarily stressed and his ability to work is reduced. Likewise, an overloaded equipment will cause malfunction or product defects.
The main causes of Muri can be summarized as follows:
- Poorly organized workstation, incorrectly designed layout, excessive effort by employees on ordinary activities
- Non-standardized work – Problems with maintaining 5S, lack of standards of maintenance, improperly used equipment, unclear instructions, poor communication also overload workers.
- Mura – Changes in production volume – extreme stress on workers and machinery causes defects and delays in the process. Overload prevents employees and machines from working to their maximum capacity, causing errors and preventing the just-in-time production target from being achieved.
3.MURA (Variation, Uneveness)
It is the irregularity in the volume of production. Changes in production planning may be due to work speed and irregular production workload.
One of the main reasons for Mura is thought to be the batch logic adopted by most companies. The multiple production philosophy aims to minimize unit cost and creates problems by limiting the company’s ability to react to changes.
Uncontrollable Mura prevents just-in-time production. Applying the just-in-time principle is only possible with a stable and non-uniform production volume. Elimination of Mura is seen as one of the biggest challenges in Lean organizations.
References
[1] Pieńkowski, M. (2014). Waste measurement techniques for lean companies. International Journal of Lean Thinking, 5(1), 9-24. [2] Bicheno, J. (2018). Towards reducing queues: Muri, Mura, Muda. In Dinis-Carvalho J, Alves AC, Costa N, Lima RM, Sousa RM (2018) Lean educator’s role in lean development. In: Proceedings of the fifth European lean educator conference (ELEC2018), Braga, Portugal (pp. 141-150). [3] Patel, D., Ranpuria, H., Shah, J., & Fournier, J. (2013). The Book Of Value Stream Maps I. Mason: The Evsm Group.